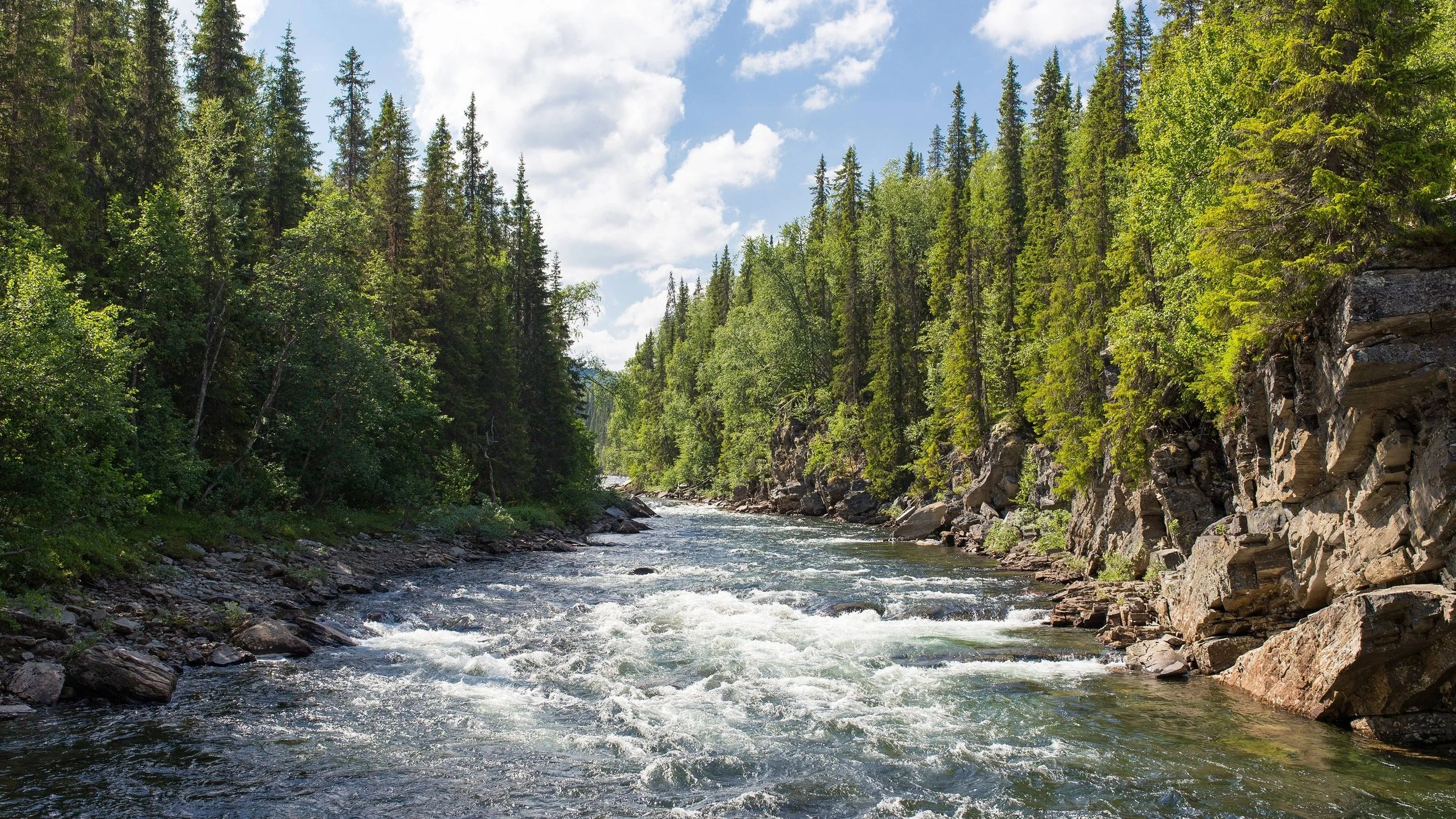
At OPC, sustainability is not just a buzz word, sustainability IS our business.
Our carbon is a 100% natural organic product, and carbon is the key ingredient to our existence on earth.

We are fully committed to making a meaningful impact in our effort to protect the environment across our entire product cycle—
From using only fallen and decaying tree stock, to creating pure organic carbon using vacuum technology (creating zero air pollution), to using our product to dramatically enhance plant growth (while reducing the amount of fertilizer and water needed), to creating carbon credits which inspire our partners to do the same.
As such, we are a carbon-negative company as the amount of CO₂ emissions we remove from the atmosphere is far larger than the trace amount of CO₂ we may create.
Our impact is undeniably positive, meaning we’re actively involved in undermining climate change while dramatically enhancing plant growth and a greener planet.
-
OPC’s original parent company, founded 12 years ago, had a single mission, to develop a natural organic carbon solely for enhanced water purification without the use of reverse osmosis. That mission was achieved with the time, efforts and help of the University of Nevada (LV). We have invested more than $20 million over those years to perfect a product which would bind and trap heavy metals, pathogens (e-coli and salmonella) and nearly all toxins. We later discovered that the attributes which created its efficacy in water were transferable to its use in natural soils and for the purpose of agricultural yield enhancement.
Most importantly we have been able to achieve what more than 100 US based “organic carbon” and ‘biochar’ makers have not. To the best of our knowledge, most, if not all of our “competition” produces their products from “biomass” power plants which generates simple “boiler ash”. What immediately sets us apart from our competition is our ability to maintain 400 square meters of surface area per gram in our carbon. This extraordinary surface area capability becomes an incredible home for microbials to flourish and grow. Every pound of our organic carbon possesses both cation/anion exchange capability. Due to this ability to create both positive and negative charges in “live” and / or organic soils, we are 100% confident any grower using our carbon, as instructed, will experience dramatically enhanced plant yields.
-
100% organic carbon made exclusively from wood cellulose (North American Pine). Typically 90% pure organic carbon, 1% ash, balance moisture.
OMRI Certified
Patent protected technology (US & Canadian)
-
Manufactured in North America
-
To promote plant growth via soil amendment and water retention allowing for nutrients to bind directly to the plant root system via “cation/anion” exchange. Nutrients bind to the carbon so as not to be leached away by rain or irrigation and the roots are “electrically” charged drawing nutrients from the carbon as needed.
-
What makes our carbon superior to our competitors is simple: we maintain a typically 90% organic carbon content as compared to our competitors’ carbon of 40% or less due to their much lower burning temperatures of 350-400 degrees Fahrenheit. By contrast, OPC, which uses only organic wood cellulose from only North American Pine trees, burns at significantly higher temperatures for much longer periods of time. Our process keeps the cellular structure of the wood intact and thus prevents our carbon from turning into useless ash.
When cultivators state they must “activate” or “charge” their carbon, this refers to the composting process in which microbes can grow, eat the harmful lignins and tars, and dramatically enhance the growth of microbials in the soil. OPC contains zero lignins, tars, zero contaminants and provides a home for microbes to flourish. To best activate OPC in “live” soil, it should be well mixed up to 5 days prior to planting, as a result, the microbes will increase in numbers and in turn fertility and yield will increase. Microbes improve the ability for the plant roots and nutrients (like NPK) loaded with carbon to interact and thus prevents them from leaching away from the plant roots. Inferior carbons have none of these attributes.
Our OPC provides the “cation/anion” exchange properties not found in any of our competitors whom we are aware of despite their claims. With both negative and positive charges which communicate directly with plant roots, our carbon releases the stored nutrients to the plants as needed. As a small note, OPC holds 3-4 times its weight in water thus maintaining soil moisture longer and requires less watering. Also due to the efficacy of our carbon, we anticipate less fertilizer (nutrients) will be required. Anecdotally, our customers have claimed that insect infestation, mold and mildew are near nil.
Lastly and most importantly, our product binds toxins, pathogens, and heavy metals occasionally found in all soils, eliminating this risk to the plant and consumer.
The 4 most important differentiations which make our patented technology far superior to all other "organic" carbons are attributable to four major factors:
-
1. Residence Time
"Residence time" of the wood cellulose in our pyrolysis kilns ("reactors" in other technologies)
-
2. Use of a vacuum
Our use of a vacuum in the kiln to deprive the chamber of oxygen for prolonged periods
-
3. Pyrolysis temperatures
Pyrolysis temperatures are significantly higher
-
4. Consistent wood cellulose feedstock
Consistent wood cellulose feedstock which is only made from North American Pine.
The vacuum technology is most important because if oxygen is present in the kiln at the temperatures we operate within (600 degrees C for clean wood cellulose derived from fallen Ponderosa, Lodgepole and Yellow pine trees), the wood cellulose would quickly turn to ash. Many, if not all of the competition we are aware of, are producing their "organic carbons” from waste or treated woods, sources well known to contain toxins and deleterious impurities. Their typical carbon content does not exceed 40 % (balance ash). Our product analysis historically runs 90% carbon, 1% Ash, 9% moisture. Our exclusive process keeps the cellular structure of the carbon intact which in turn allows for its surface area to allow microbials to inhabit and grow. It is this growth of microbials which enhances plant yield.
Of note, residence time in our pyrolysis units is between 8 to 10 hours (think of a modified slow pyrolysis). This long residence time allows for the total removal of tars, lignins, and other impurities from within the cellular structure of the wood. Also, the long residence time at these high temperatures impart exclusive properties into the carbon matrix as a result. In addition, we operate at the optimal temperature to impart the "cation exchange" property into the carbon matrix. The cation exchange property binds heavy metals permanently. The carbon ‘positive’ charge absorbs ‘negatively’ charged nutrients but allows the plant roots to absorb the nutrients as needed. As an additional benefit to the long residence time, we also convey the "anion exchange" property into parts of the carbon matrix as well. As an aside, the USDA confirmed that our organic carbon is nearly alone in a space of hundreds tested which has both properties present, a near anomaly. Cation is important in absorption of heavy metals, unwanted nutrients, etc. Anion allows us to absorb salts. The long residence time allows us to use varied North American Pines as feedstock and also allows us to overcome the potential non-uniformity of those feedstocks. Uniformity means consistency of product.
By contrast, our competitors take non-uniform wood (and other unidentified biomass) feedstocks like wood chips and sawdust and attempt to apply a uniform process constantly moving the material through a reactor, usually for a minute or less (think of fast pyrolysis). As would be expected, they end up with a mix of qualities in the results. The lack of residence time does not allow for complete removal of impurities from the cellular structure, so they may end up with toxins and heavy metals embedded in their carbons. Some "organic" carbon producers attempt to make up for the quick process time by increasing the temperatures of the reactors to get quicker conversion, which requires them to often use stainless steel in the reactor (we only use mild steel in our kilns). Stainless steel leaches nickel into the carbon at high temperatures, so they are potentially adding toxicity to their carbons. The greatest problematic issue nearly all of our competitors face is the simple fact that they begin their process with feedstock from “biomass boiler ash”. This feedstock is typically devoid of anything but ash and extremely low in pure carbon. More significantly it produces no cation or anion exchange, effectively suppressing microbial growth which undermines yield enhancement. Lastly, many of our competitors are attempting to monetize their syngas or condense bio-oil from the process, which then converts their carbon into a residue. When they pursue the gas and oils, it means they are operating at a temperature level that ensures toxic residues will ultimately end up in their product, which in turn, will undoubtedly end up in the plant.
OPC is quite confident that our technology is vastly superior to all North American competition from either “organic carbon” producers or “biochar” makers. Our 17 patents support our view as does the enhanced yields, suppressed toxins and consistency of our production.
Mix 1 cup of OPC per gallon of natural live soil, 5 days before planting.
We highly recommend using microbes of your choice
OPC does not work in hydroponic, Rockwool, or inorganic suspension material.
Water, fertilize and provide sunlight to plants as always.
Expect an increased yield as well as the suppression of pathogens, heavy metals, mold, and most insects
Very Simple Instructions
“To whom it may concern,
As a Ph.D. in the field of Environmental Engineering, with experience for over 28 years in water quality, water treatment, and site restoration, after being asked to confirm the properties attributable to the organic carbon subject of this correspondence, I can say that it has attributes which have been found in only a small fraction of the myriad carbons my research group has tested.
These attributes include specific surface characteristics and their accompanying abilities to bind various organic pollutants [1], nutrients [2], and heavy metals [3] found in water with an outstanding potential for water treatment. We also have observed its ample capacity to release nutrients and organic matter [2], which may be associated with its remarkable ability to enhance plant growth when utilized with the proper ratio of carbon to soil.
In agreement with my research, these remarkable characteristics makes this organic carbon unique and worth exploring other potential applications. We have found it very useful as a support for nano-sized materials in water treatment applications [4], highly valuable filter media for stormwater treatment basins [3], or as valuable media for translating nutrients from water bodies into crop fields [5].
Please do not hesitate to contact your sales agent to find out by yourself the outstanding characteristics of this material and figure out the applications that better match with your needs.”
Sincerely,
— Erick R. Bandala, Ph.D., P.H.
Testimonial from an
Environmental Engineer
References
[1] A.M. Clurman, O.M. Rodríguez-Narvaez, A. Jayarathne, G. De Silva, M.I. Ranasinghe, A. Goonetilleke, E.R. Bandala, Influence of surface hydrophobicity/hydrophilicity of biochar on the removal of emerging contaminants, Chem. Eng. J. 402 (2020) 126277. https://doi.org/10.1016/j.cej.2020.126277.
[2] N. Hong, Q. Cheng, A. Goonetilleke, E.R. Bandala, A. Liu, Assessing the effect of surface hydrophobicity/hydrophilicity on pollutant leaching potential of biochar in water treatment, J. Ind. Eng. Chem. (2020) 222–232. https://doi.org/10.1016/j.jiec.2020.05.017.
[3] N. Hong, Q. Cheng, B. Wijesiri, E.R. Bandala, A. Liu, A. Goonetilleke, Integrating Tank Model and adsorption/desorption characteristics of filter media to simulate outflow water quantity and quality of a bioretention basin: A case study of biochar-based bioretention basin, J. Environ. Manage. 304 (2021) 114282. https://doi.org/10.1016/j.jenvman.2021.114282.
[4] S. Mortazavian, T. Jones-Lepp, J.H. Bae, D. Chun, E.R. Bandala, J. Moon, Heat-treated biochar impregnated with zero-valent iron nanoparticles for organic contaminants removal from aqueous phase: Material characterizations and kinetic studies, J. Ind. Eng. Chem. 76 (2019) 197–214. https://doi.org/10.1016/j.jiec.2019.03.041.
[5] A. Smolinski, A. Zeidman, E.R. Bandala, Chemically Exhausted Biochar as a Sustainable Replacement for Chemical Fertilizers, in: 2021 NV INBRE Statew. Annu. Meet., 2021: p. 30.